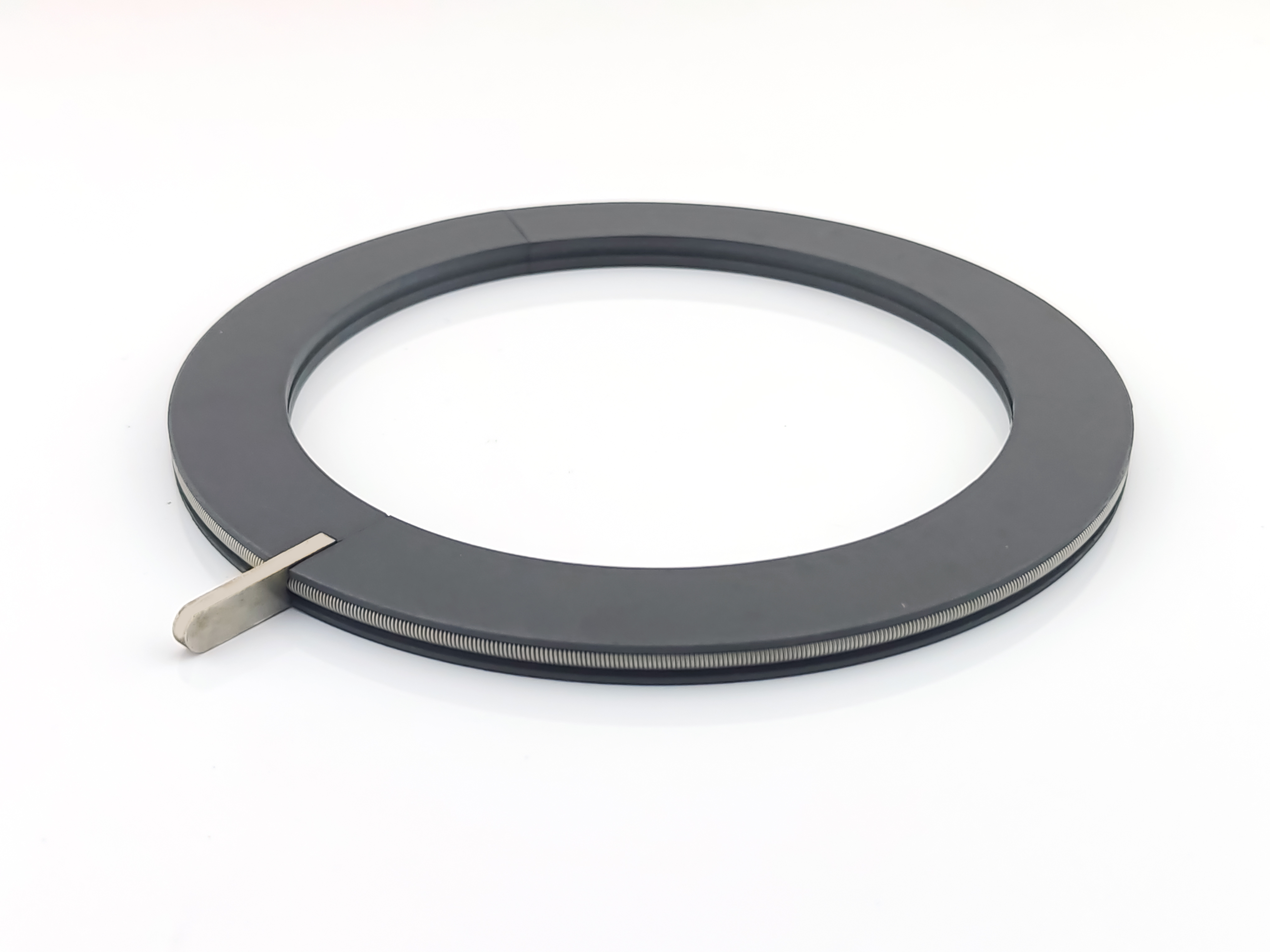
In compressor rotary systems, sleeve bearings serve as critical bridges connecting rotating shafts and static housings. As precision components supporting crankshafts or rotor shafts, their performance directly determines equipment vibration control, transmission efficiency, and operational lifespan.
I. Structural Design: Multi-Layered Functional Integration
Layer |
Material |
Function |
Critical Parameters |
Steel Backing |
45# Steel / Alloy Steel |
Structural support |
Thickness: 3-8mm |
Copper Alloy |
ZCuSn10P1 / ZCuAl10Fe3 |
Heat dissipation Vibration damping |
Thermal conductivity: 60-80 W/(m·K) Compressive strength: 250-600 MPa |
Polymer Surface |
PEEK+CF / PTFE-based |
Low-friction interface |
Operating layer thickness: 0.5-3mm Dry friction coefficient: 0.04-0.15 |
Oil System Features:
- Helical/groove oil channels covering 15-25% surface area
- Minimum oil film thickness: 15μm @ 3,000 rpm
- Precision tolerance: H7/k6 grade
II. Material Evolution: Engineering Plastics Revolution
Metal-Based Bearings (Conventional)
- Tin Bronze (ZCuSn10P1): Oil-dependent, limited to ≤1800 rpm
- Aluminum Bronze (ZCuAl10Fe3): Higher load capacity, suitable for ≤3500 rpm
Engineering Plastics (Advanced Solutions)
- PEEK + 30% Carbon Fiber:
- Continuous operating temp: 260℃
- PV limit: 3.8 MPa·m/s
- PTFE Self-Lubricating:
- Chemical resistance to acids/alkalies/solvents
- Cold start capability: >100,000 cycles
Nanotech Enhancement: WS₂ nanoparticles reduce friction to μ=0.03
III. Core Functions: Multi-Dimensional Protection
- Precision Positioning:
Limits radial runout ≤0.05mm, vibration attenuation >85%
- Friction Management:
- Forms hydrodynamic oil film (lubricated systems)
- Develops PTFE transfer film (oil-free compressors)
- Thermal Regulation:
Copper alloy dissipates heat 5x faster than polymers
- Safety Sacrifice:
Deliberate plastic deformation protects shafts during overload
IV. Installation & Maintenance Essentials
- Fit Requirements:
Interference fit: 0.05 + 0.001D mm (D=shaft diameter)
Axial clearance: 0.2-0.5mm
- Failure Warning Signs:
- Adhesive wear (poor lubrication)
- Abrasive scratches (oil contamination)
- Fatigue spalling (overload operation)
V. Future Technology Trends
- Smart Bearings:
Embedded sensors monitor:
- Real-time oil film thickness
- Temperature gradients
- Functionally Graded Materials:
3D-printed with layered properties:
- Surface: 100% self-lubricating polymer
- Core: High-strength alloy
- Industrial Validation:
Nano-enhanced sleeves show <0.03mm wear after 20,000 operational hours
[DLSEALS kindly Reminder] Sealing issues? Turn to DLSEALS! As a sealing component manufacturer, we specialize in customizing sealing components, providing a full range of services from design, research and development, production, testing, and more. If you have more information you'd like to know, feel free to contact us directly. DLSEALS's product experts are dedicated to serving you!